Mark in Action Winners' Stories: BAC team
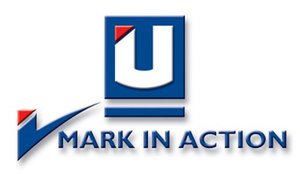
Mark in Action celebrates colleagues who demonstrate The Unipart Way in the way they think, work and behave to deliver value for our customers.
A recent Mark in Action, awarded to two colleagues in JLR’s Battery Assembly Centre (BAC), is a great example of how they took time to deeply understand their customer’s needs and, as a result, proactively identify and develop solutions to help keep their operation moving.
Unipart’s operation in the BAC provides storage and parts to the production line for car batteries. The provision of the correct parts to the battery assembly line is crucial to a smooth production schedule.
Stock Operations Manager Krzysztof Jachnicki and Materials Replenishment Coordinator Shahin Shirazi identified a lack of a systemic parts compliance check for parts going to the point of fit on the production line. This created opportunities for errors with parts being scanned to an incorrect location without a system to flag when this had happened.
Aware that such errors had the potential to lead to stock integrity issues, lost stock and impact to the customer’s production schedule, Krzysztof came up with the idea of creating a digital dashboard that would highlight any product scanned to an unexpected location.
Shahin and Krzysztof were newly promoted to their respective roles, but took the initiative and researched a technical solution that was outside of their existing expertise.
They developed a way to combine data sets to run in JLR’s warehouse management system and run the scripts automatically once initiated.
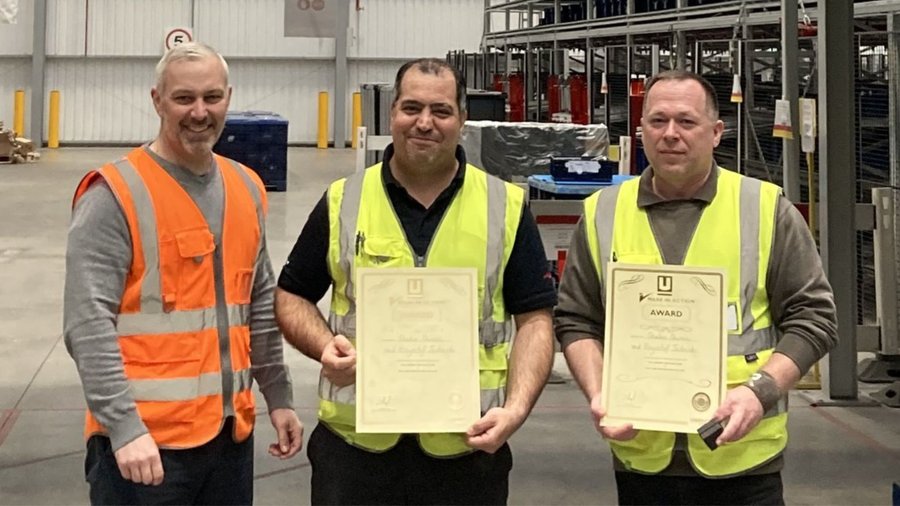
A physical dashboard was developed to not only display the initial error, but also the correct location the product should be delivered to. Emails are automatically generated to the correct audience so that the issue can be quickly rectified.
This solution is now in constant use at the BAC as a discrepancy report and has correctly identified incorrect scans that have prevented any impact to the customer.
Senior Operations Manager Les Earp nominated the pair for the Mark in Action Award.
Les said, “Krzysztof and Shahin sought out knowledge and used new technologies, even working on it in their own time. Innovation such as this demonstrates our commitment to the customer, their business and to the principles of continuous improvement. JLR have increased confidence that the right part will be in the right place at the right time. This also saves time during stock counts and inventory counts as issues are identified and can be corrected in real time.”
"Krzysztof and Shahin’s work has showcased the capability, drive and customer commitment of our colleagues which can only be achieved through excellent employee engagement. I'd like to give my sincere thanks to Krzysztof and Shahin for this outstanding piece of work. We have been working with other Unipart sites to see if this solution could support other operations, and JLR have been delighted with this innovation and Unipart’s commitment to helping them to solve problems.”
3 comments have been posted.
March 29, 2025, 2:48 a.m. - Stewart Chapman ¶
March 28, 2025, 9:17 p.m. - Steven Lacey ¶
March 28, 2025, 8:18 a.m. - Les Earp ¶