Go Wednesday: Dan Powers an effective Warehouse Management System
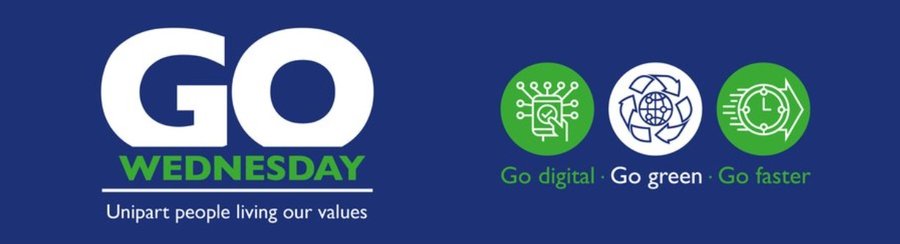
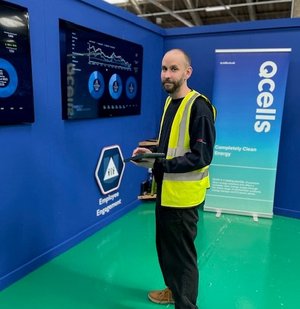
Warehouse Management Systems are the bedrock of an effective logistics operation, and are used across Unipart to deliver the customer promise.
The Q-Cells contract at the Unipart Logistics Honeybourne was without a Warehouse Management System (WMS) until Team Leader Dan Powers used self-taught data skills and the problem solving approach of The Unipart Way to create one.
Dan’s WMS has increased the visibility of data and taken the site from ad-hoc hell to a data-driven dream team, enabling them to further support the Policy Deployment Matrix Level 0 Aim of ‘Improving customer experience and satisfaction.’
We spoke to Dan to find out how his mix of apprenticeship study and self-learning enabled him to develop the solution: “I love data and solving problems. The Q-Cells contract at Honeybourne had no Warehouse Management System or monitoring. You'd have to literally go down to the area to see what's happening there.
“Using my apprenticeship studies, I built a Looker Studio data suite, starting with things such as pallet count, the number of deliveries, and collections. And then it progressed…We now use the software across different contracts within the site. It shows us our outstanding orders, audits, future activity, and historic trends.”
The improvements haven’t stopped there. Steve Thomas, Operations Manager, said: "It’s a fantastic tool that Dan’s built. It’s had a massive impact on what we can do, and what we can deliver on a day-to-day basis. It gives me a really good start of the day from a planning point of view.”
The team has created an Our Contribution Counts circle off the back of this project to share best practice with other Unipart colleagues. Steve said: “We've talked to the customers, involved stakeholders, and improved our processes. Without the visibility of the data, and the way that Dan has put it across, I would never have seen that before.”
Talking of customers, and Unipart’s promise to understand their real and perceived needs and serve them better than anyone else, Dan said: “When I started to create this, we didn't really have a great deal of visibility of where stock was, nor any Warehouse Management System.
“There was also a lack of service levels agreements with the customer too, so it was very much ad hoc. We now have processes in place with the customers and have created consistency, and improved customer experience and satisfaction, which is also aligned with the PDM.”
Unipart Logistics Managing Director Ian Truesdale saw the new WMS in action at a recent visit to Honeybourne. Ian said: "One of my favourite parts of my job is getting out onto our sites to see all the great work that our colleagues are doing to deliver our customer promise.
“I visited the Battery Assembly Centre (BAC) and Honeybourne for the first time, and was given a fantastic tour of both sites. I saw a great example of how a colleague made a difference by building a Looker Studio data suite in Honeybourne to monitor the performance in the Q-Cells contract."
If you have any ideas for a Go Wednesday story please contact us at unipart.group.communications@unipart.com
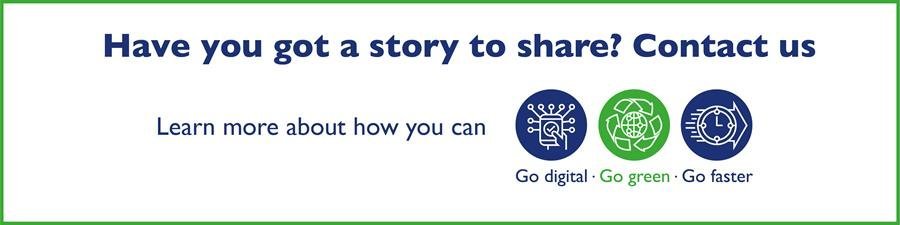
4 comments have been posted.
Aug. 4, 2023, 9:38 a.m. - Adrian Wilde ¶
Aug. 3, 2023, 10:06 p.m. - Catherine Guild ¶
Aug. 3, 2023, 8:25 a.m. - Joanna Matson moderator ¶
This comment has been removed.
Aug. 3, 2023, 8:25 a.m. - Joanna Matson moderator ¶
Aug. 2, 2023, 8:25 a.m. - Mark Timbs ¶