Go Wednesday - The Unipart Way transforms warehouse efficiency
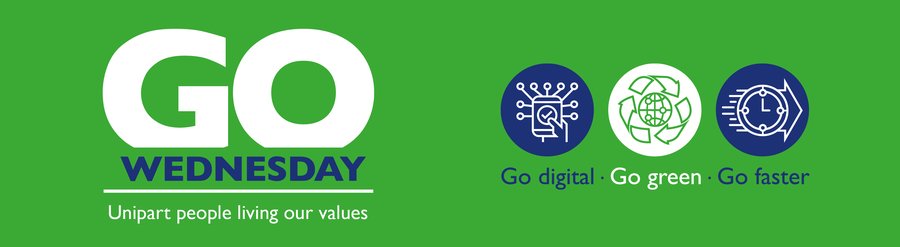
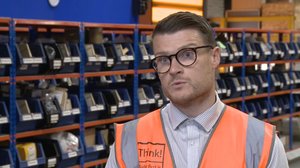
The team at Unipart Rail’s National Distribution Centre in Doncaster decided they wanted to make a step change to the service they provide their customers. So, they called in the support of The Unipart Way Practitioner team, and implemented the tools of The Unipart Way, to find a solution that would transform their processes.
Back in 2019, two previously separate operations within the centre were merged into one, but continued to operate as separate entities, each with their own service-level agreements (SLAs), teams, and processes. This was causing a silo mentality, and preventing effective best-practice sharing and cross-functional working.
Michael Forrest, Unipart Rail Continuous Improvements Manager, explained how this incohesive setup was affecting performance for the customer: “After analysing our Outbound picking process, the diagnostic identified 3,054 hours of waste per year, equivalent to an additional 24,575 picks per year with the same resource, or a 12% productivity increase.
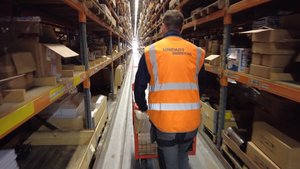
“We discovered that by eliminating this waste, process capacity could be increased without the need for an increased headcount, which is particularly prevalent considering the expected infrastructure material sales increase of up to 45% in 2022.”
The team used the tools of The Unipart Way to try and merge the two processes together. First, they utilised the Creative Problem Solving (CPS) methodology, using tools such as value stream mapping and baseline data analytics to better understand resource capacity.
Michael explained how the tools made life easier for the team: “The tools and techniques of The Unipart Way were used throughout the project, from identifying the key opportunities and challenging the status quo, right through CPS activity.
“Project level Comms Cells were developed, and supporting metrics were established to show our progress and mitigate any issues. The project team was also very focused on the end-to-end customer experience, which was at the forefront of the future state solution design."
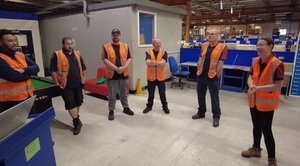
Through the use of these tools, the team discovered a large amount of motion waste, as most of the fast-moving material was located at the top-end of the inbound, causing significant time delays. Therefore, the team brought the fast-moving material to the outbound packing area, reducing the motion waste.
From this project, the team have found two key improvements. Firstly, a dedicated ‘Fast Pick Zone’ has been positioned as close as possible to the Outbound area, enabling the removal of 2,328 hours of non-value added activity, and 726 hours in motion waste.
Secondly, a singular Outbound process will be created to utilise the most effective aspect of each process, and create a truly aligned, efficiency-focused operation.
These improvements would not have been possible without the whole team working together. Michael said: “It was vital we engaged the team on the shop floor, through tools such as Insight Stars, to ensure the right ideas were being put forward in an environment of empowerment and ownership for all colleagues.”
If you have any ideas for a Go Wednesday story please contact us at unipart.group.communications@unipart.com
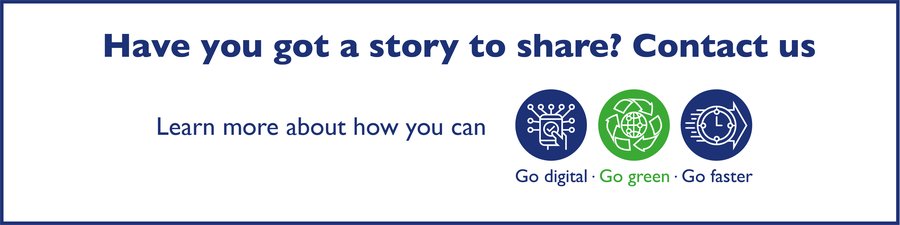
5 comments have been posted.
Oct. 12, 2023, 8:36 a.m. - Christina Cotter ¶
Oct. 11, 2023, 8:47 a.m. - Fiona Hately ¶
Oct. 11, 2023, 8:47 a.m. - Peter Wing-Young ¶
Oct. 11, 2023, 7:32 a.m. - Gemma Peters ¶
Oct. 11, 2023, 7:23 a.m. - Charlie Brown ¶