Mark in Action: OCC improves accuracy and end-customer satisfaction
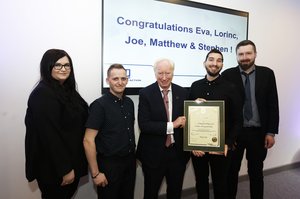
A team, made up of Joe Merry, Lorinc Illes and Stephen Wootten and led by Matt Ryan and Eva Halagardova from UL Burton were recognised by Mark in Action for their contributions to an OCC for Unipart Logistics’ customer Waterstones, based in Burton-on-Trent.
When the site moved to the Blue Yonder last year, following investment and development by the customer, the pick error rate on tote checks was around 3%. In a bid to improve accuracy of their processes, the team implemented a number of solutions, with each Mark in Action winner taking ownership of an element. As a result, around 125,000 more units are now sent to the correct place…
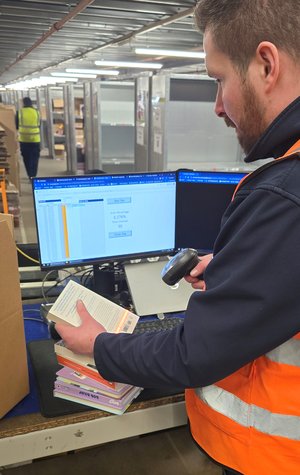
On-Site Stock Manager, Eva Halagardova, identified that the method to capture the site’s tote accuracy had waste. The check also had its own accuracy problems, due to a reliance on concentration, being paper based and very time consuming. With large numbers of totes required to be checked, this method wasn’t viable.
Joe Merry is the digital champion on site and digitised the tote checks, making it quicker and more accurate, as well as automating the process where he could: “The amount of time taken to run the reports the old way with paper forms took over eight hours. Moving it onto Excel, and scripting the sheets so that it worked automatically, reduced the time taken to under four.”
Along with team leader Steve Wootten, Lorinc Illes, Problem Resolution Expert, completed an Insight Star, in order to find parts of the process that may be causing the errors, and engaged colleagues in the correct ways of working: “We noticed that the Visual Management was a bit overwhelming. There were barcodes too close together, which meant the wrong ones were scanned. We added an explanation next to the barcodes, and what to use them for, which made it easier for colleagues.”
As a team leader, Steve Wootten is also responsible for workforce management, and uses Joe’s reports to communicate and investigate with his team. He is currently completing his Gate to Great programme, and using the tools learnt around behaviours to drive improvements:
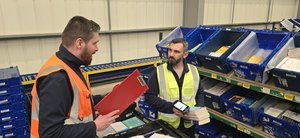
“There was a moment where we saw a small spike in errors, so I went out with one of the trainers and did some analysis of where the mistakes were happening. We realised that some users were processing errors incorrectly, which in turn doubled the number of incorrect items rather than resolving the issue they had. Once we informed and worked with the colleagues involved, the error rate lowered again.”
The team doesn’t intend on stopping at their improved error rate of 0.5%, as Matt Ryan, Shift Operations Manager, shares: “The next step is to try and trend under 0.4%, which will be our new service level agreement (SLA) once the relevant budget has been signed off. We’re still working on the process and have weekly meetings with the customer, where we can share our trend lines and our improvement focus points from the data that we’re gathering.
“The stock is now in a much better position - we’re keeping to SLAs. We’re not having to do as many adjustments because we’re getting it to the right place first time rather than having to rework it, and the team themselves are more engaged.”
The full Mark in Action ceremony from March 2024 is available to watch with this video link.'
Let's not underestimate the huge difference that you made
Closing the Mark in Action ceremony, Chairman John Neil, commented on the impact on Waterstone’s end customers, saying: “If you were a customer and you were going in to get the book you’d been promised, maybe for a birthday present, or maybe something you really wanted to read, or maybe need for an exam, and it had not been delivered - you’d be pretty upset, and angry and go ‘maybe next time I’ll get from somewhere else’. So let's not underestimate the huge difference that you made by fixing the system.”
To nominate a Unipart employee or team for a Mark in Action award click here.
1 comment has been posted.
April 19, 2024, 10:29 a.m. - Catherine Guild ¶